Towards greener, safer construction: how mechanical splices has become a powerful tool in the fight against climate change ?
In 1988, LINXION introduced a major innovation to the construction industry: mechanical splices. This revolutionary method not only redefined safety standards, but also paved the way for more sustainable and environmentally-friendly construction. The traditional method of overlapping no longer seems the most attractive.
But how can a simple mechanical splices achieve a safer construction than traditional cladding? And how has it become a powerful tool in the fight against climate change?
Reinforcement connections in the face of overlap
What are overlaps or mechanical splices ?
Two reinforcing bars are placed so as to overlap over a certain length. The length of this overlap, known as the overlap length, is calculated according to the structural requirements and the properties of the concrete and steel.
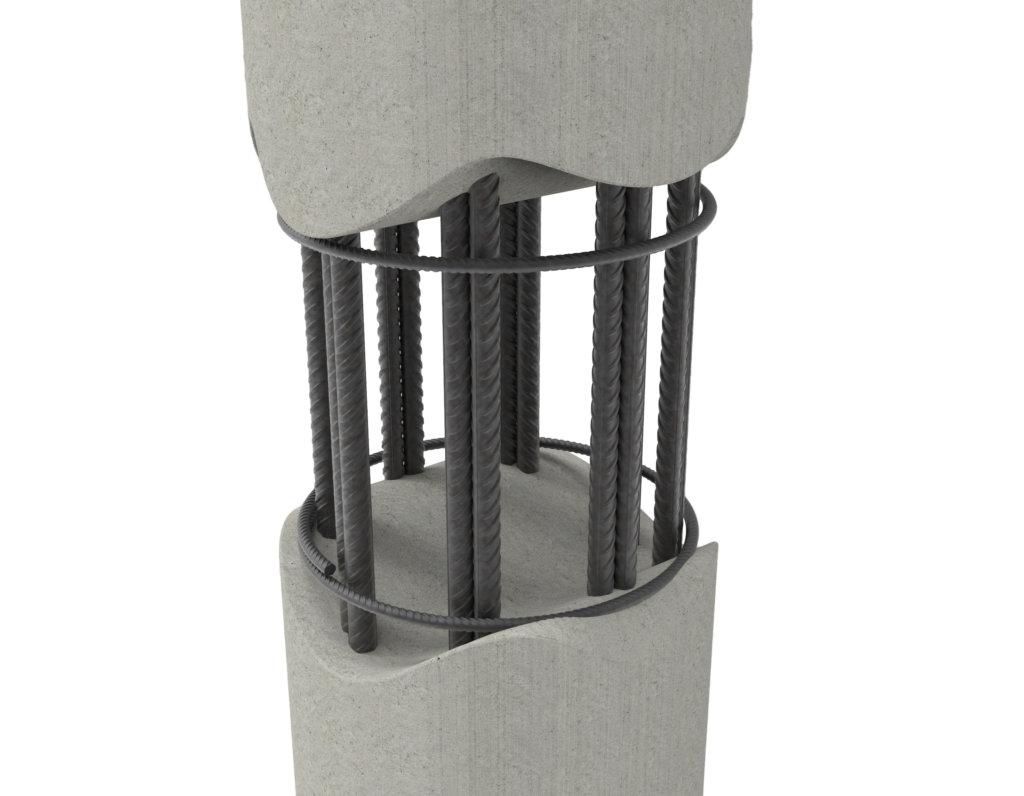
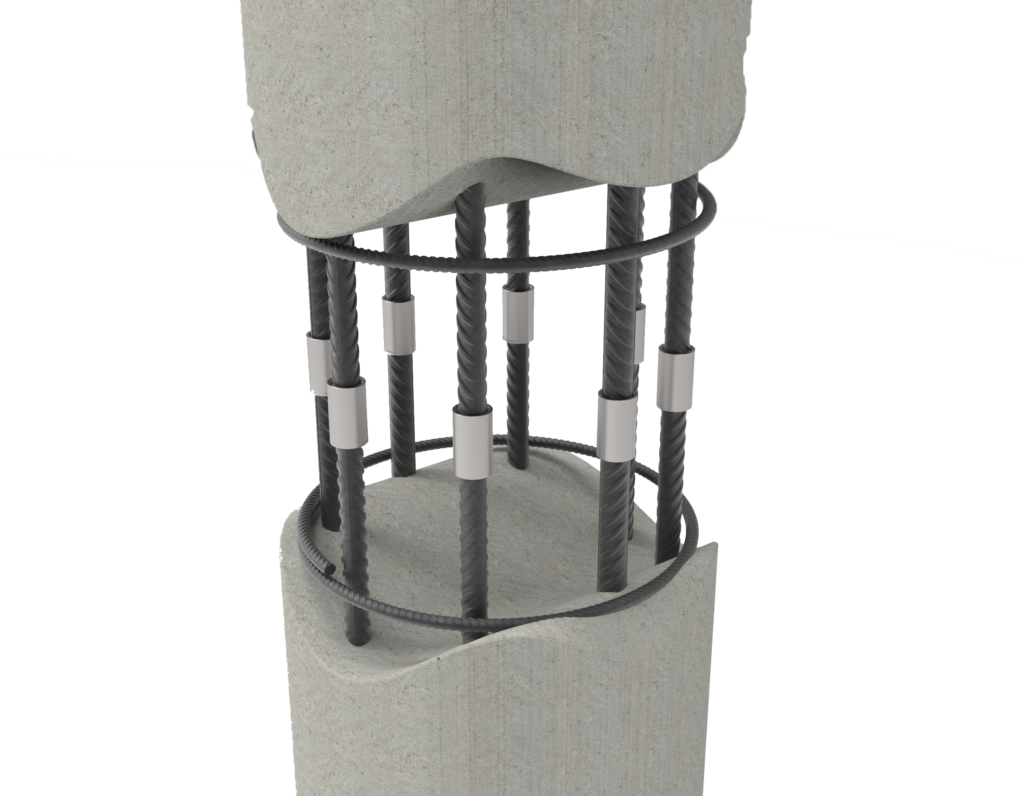
Mechanical splices
Mechanical splices use devices such as sleeves, threaded connections, clamps or crimping systems to connect the bars.
Certified mechanical splices for optimum safety
Numerous certifications exist worldwide for testing and securing rebar connections. The technical specifications required are extremely precise and demanding. However, according to EUROCODE2, a simple steel cover is sufficient for construction purposes.
There is no specific certification for covering. No tests are carried out to verify the safety of the cladding.
superior safety
The traditional overlapping method and mechanical splices are two quite distinct techniques. They differ significantly in terms of performance and reliability.
Overlapping transfers the load directly through the concrete. This method involves superimposing bars over a certain length, where the concrete plays a crucial role in transmitting forces.
However, this technique has one major weakness : in the event of impact, the structure loses its integrity and often breaks at the overlaps, jeopardizing the stability of the whole.
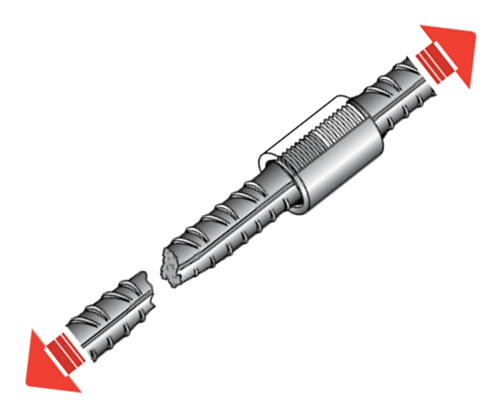
In contrast, mechanical splices offer a much more robust solution. Here, the load is transferred directly by the mechanical splices of the coupler, which firmly fixes the reinforcing bars together.
In the event of an impact, the coupler guarantees the integrity of the structure, as it provides the same mechanical characteristics as a continuous reinforcing bar along its entire length.
In this way, reinforcement connections maintain structural cohesion and performance, even under dynamic loads, offering superior reliability for projects requiring high safety standards.
reinforcement connections, a more environmentally-friendly construction method
The STARS vision: environmentally-friendly construction with BARTEC rebar connections
STARS (Steel Reduction through Threaded Reinforcement Connections with Couplers) is a greener construction initiative.
It was born of the need to reduce CO2 emissions linked to steel consumption: one of our main concerns, and an environmental issue for the 21st century.
Thanks to this vision, we offer a different solution to traditional cladding, with reinforcement connections that immediately reduce the amount of steel within the concrete structure.
Reducing the carbon footprint at the design stage
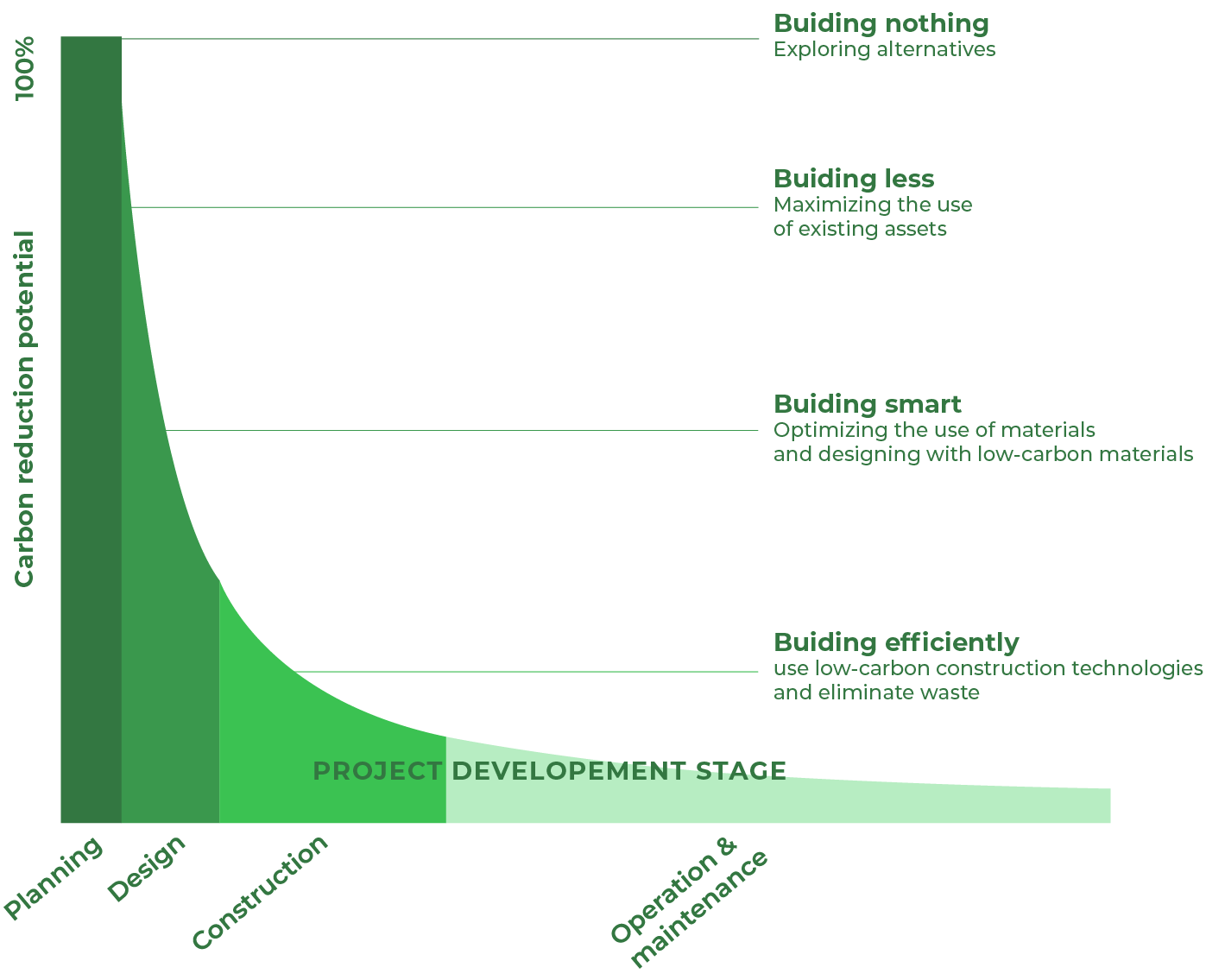
It is during the design phase of a project that the greatest influence on reducing carbon emissions is exerted.
The challenge is to find structural solutions that are both ecologically efficient and safe.
Mechanical splices, for example, eliminate the causes of inefficiency associated with cladding, such as over-consumption of steel and cost variability, while offering a new, more durable and predictable solution. In this way, connections contribute to the significant reduction of carbon emissions in construction projects.
Zooming in on a reinforced concrete structure, we have the following composition:
For over 30 years, LINXION The Original has been analyzing the impact of using rebar connections, and particularly couplers, in complex reinforced concrete structures. The results reveal a potential reduction of over 20% in the amount of steel used.
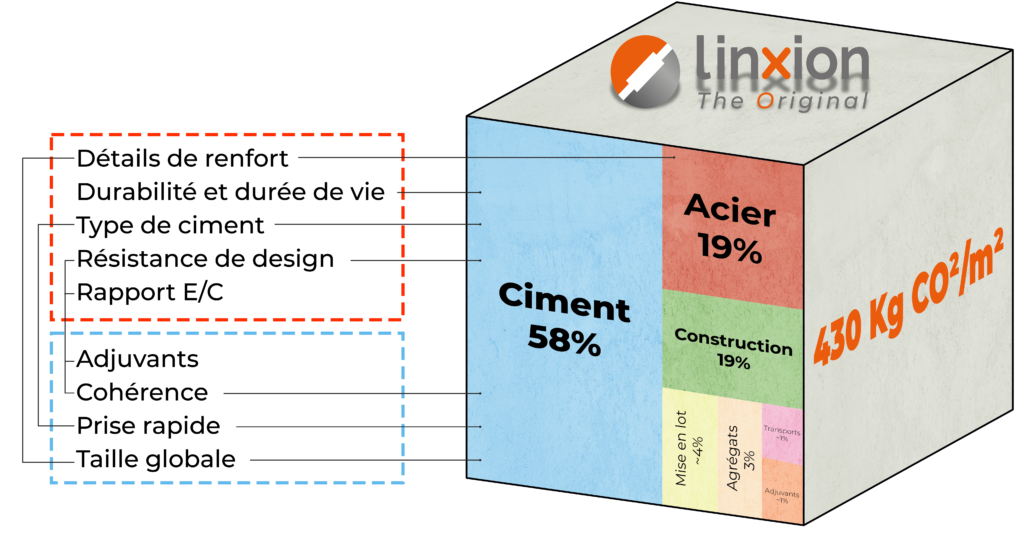
20% of 19% means: almost 4% immediate reduction in the carbon incorporated in each reinforced concrete construction.
Examples of steel savings in reinforced concrete construction
To illustrate the effectiveness of its technology, LINXION presents two concrete examples:
18-storey building
In this project, the use of 94,831 LINXION mechanical splices resulted in :
- A saving of 372 tonnes of steel
- A reduction of 688 tonnes of CO2 emissions
- A total reduction of 20% in emissions compared with the traditional method
Two-tower bridge
For this major infrastructure project, the use of 142,870 mechanical splices resulted in :
- A saving of 913 tonnes ofsteel
- A reduction of 1.688 tonnes of CO2 emissions
- A total reduction of 24% in emissions compared with the traditional method
A giant step towards sustainable construction
These two examples clearly illustrate the potential of rebar connections to transform the construction industry. By significantly reducingsteel use and associated CO2 emissions, LINXION is paving the way for more environmentally-friendly construction practices.
By replacing the traditional cladding method with rebar connections, LINXION has not only reinvented structural safety, but also set a new standard for sustainability and the environment.
LINXION is firmly committed to the fight against climate change, while offering unrivalled structural performance.
Concrete results achieved in major projects demonstrate that the adoption of reinforcement links enables a significant reduction in the use of steel and therefore in CO2 emissions.
With its STARS vision, LINXION proves that technical innovation can go hand in hand with environmental responsibility, transforming the construction industry into a key player in sustainability.
It’s time for industry professionals to rethink their practices and adopt solutions that not only guarantee safety, but also protect our planet. Together, we can build a future where construction and sustainability coexist harmoniously. Let’s embrace this green revolution and make every project a step towards a more environmentally-friendly world.