In a world where the challenges of modern construction are multiplying, the building industry finds itself at a crucial crossroads. Faced with the challenges of safety, sustainability and environmental impact, a revolutionary innovation is emerging: Mechanical splices. These devices, often unknown to the general public, play a fundamental role in the strength and durability of reinforced concrete structures.
While the traditional technique of rebar overlapping has long been the norm, it’s time to reconsider our practices. Reinforcing ties offer a reliable alternative, combining enhanced safety with respect for the environment.
In this article, we explore the benefits of this innovative technology and its potential to transform the construction industry in the long term.
1. The STARS vision: greener construction
The STARS vision developed by Linxion The Original offers an innovative ecological solution.
Today, steel production accounts for 8% of CO2 emissions. to bring the sector into line with the target “zero emissions” of 2050, emissions must fall by at least 30% by 2030. This can only be achieved by reducing the use of steel, thereby helping to reduce the CO2 emissions associated with steel production and transport.
Building also means assessing the building’s overall environmental impact. Materials must be considered as a whole, including their origin, CO2 emissions and manufacturing process. It is crucial to identify sustainable products and eliminate those that are harmful to the environment and human health, such as asbestos or lead, which are now banned.
Thanks to this vision, we offer a different solution to traditional cladding, with reinforcement links that immediately reduce the amount of steel within the concrete structure.
The Grand Paris Express project is a perfect illustration of the benefits of this approach. Thanks to the use of 320,000 Linxion couplers by 2021, the project has achieved significant steel savings. The amount of steel used has been reduced from 2806 tonnes to just 173 tonnes, a saving of 2600 tonnes, representing 4871 tonnes of CO2.
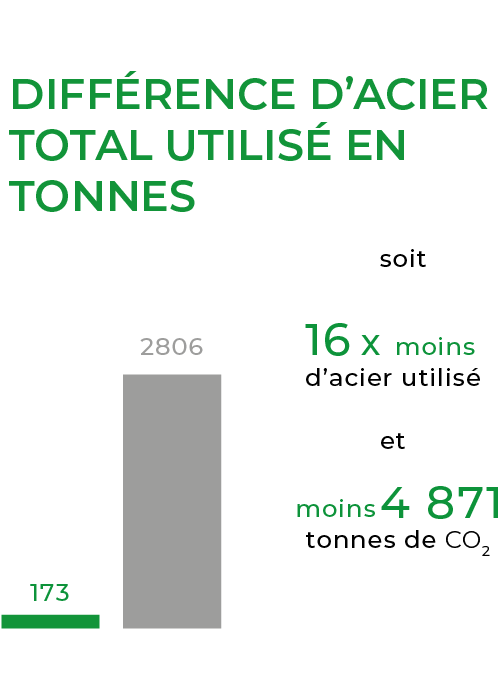
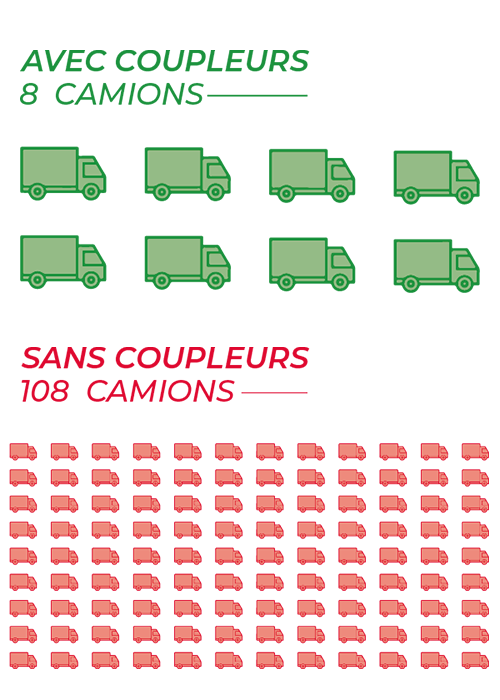
2. The advantages of connections and the limits of overlapping
Mechanical splices are distinguished by their superior reliability and safety. Unlike traditional rebar overlap, they benefit from rigorous international certifications, guaranteeing their performance. In the event of impact or disaster, these connections maintain the structural integrity of the structure, offering much higher resistance than conventional overlaps, which can break at the bar connection.
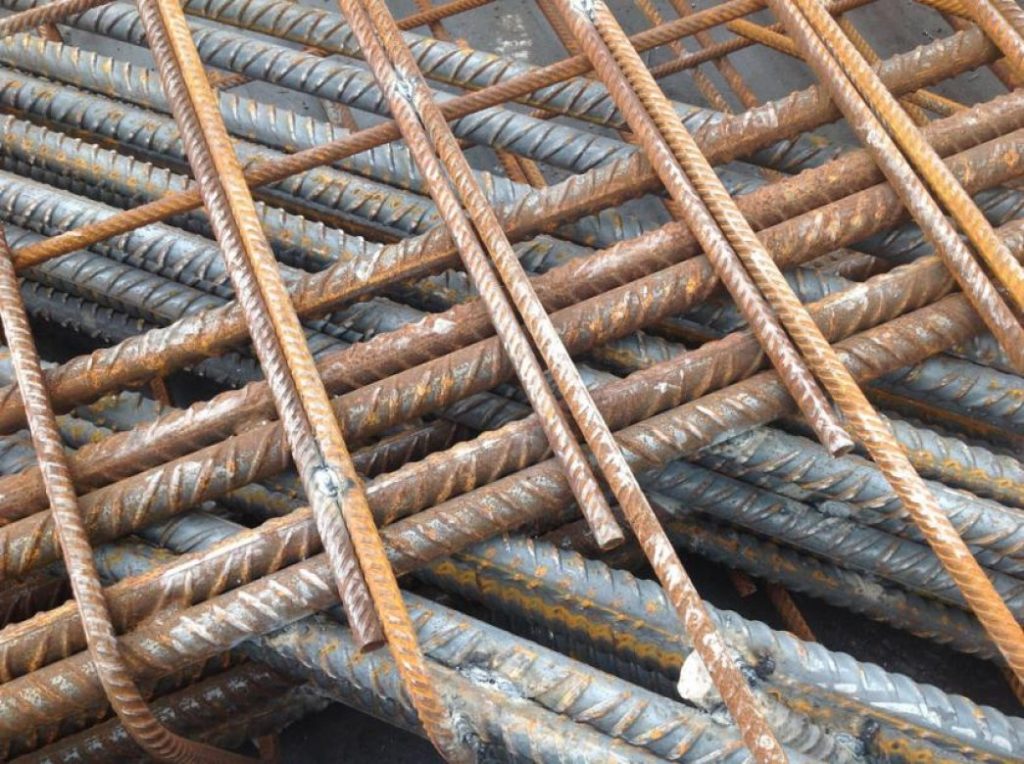
In economic terms, mechanical splices offer a clear advantage. Their final cost is fixed and predictable, unlike overlaps whose price can vary according to fluctuations in the cost of steel and the preparations required on site.
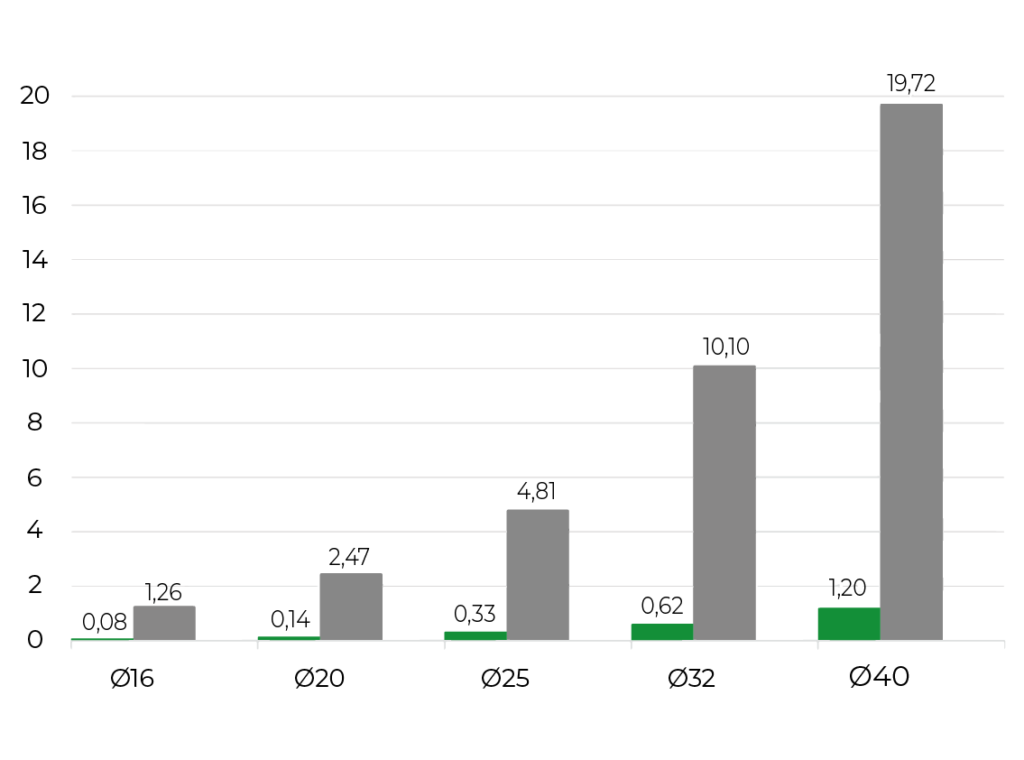
What’s more, the use of mechanical connections significantly reduces the weight of structures. A simple coupler can replace a length of overlap equivalent to 50 times the diameter of the rebar. A coupler is much lighter and ensures the continuity of the rebar.
Thanks to our STARS approach, a reduction of almost 4% in C02 emissions is possible for an entire building.
If we zoom in on a reinforced concrete structure to see the distribution of carbon incorporated in each element present, we have the following composition:
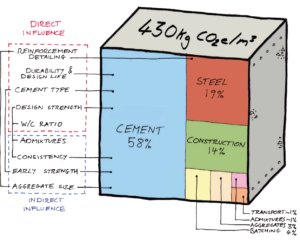
However, we have seen that it is possible to reduce steel consumption in a large project by 20% by using reinforcement links….
And that the corresponding proportion of steel in a reinforced concrete structure is around 19%.
So 20% of 19% means : Almost 4% IMMEDIATE REDUCTIONof carbon incorporated in each reinforced concrete construction
3. Why choose BARTEC by Linxion?
Although mechanical splices offer many advantages, it’s crucial to choose quality products.
Visually similar products may differ in terms of precision, control and quality.
Additional checks are therefore essential to avoid risky construction.
Linxion The Original, with its Bartec process, stands out for its commitment to quality and reliability. Unlike some manufacturers who may use inferior materials or less precise manufacturing processes for products delivered to construction sites. Linxion maintains high standards throughout the production process, from product manufacture to on-site installation.
1 coupler in 1000 undergo rupture testing, and all our components are produced to identical quality standards. Today, our products are a quality reference for the French quality laboratory Compalab.
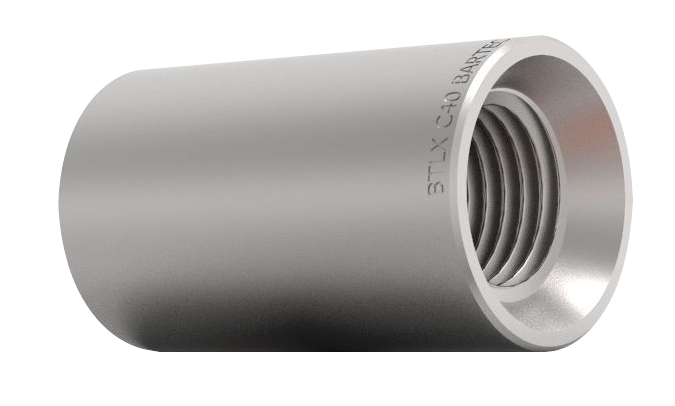
Linxion couplings are manufactured using high-quality materials and precision machinery, guaranteeing consistent performance.
What’s more, Linxion ensures proper training for the installation of its products, unlike some competitors who may neglect this crucial aspect.
The machines used by Linxion The Original are highly precise. They ensure optimal threading designed to pass laboratory tests.
They are all made in Italy by our subsidiary Cergil Industry. Whether it’s the Cold forging machine or the threading machine. These machines are designed and built for optimum thread production. Our machines are custom-built, Internet-connected and are at the forefront of innovation.
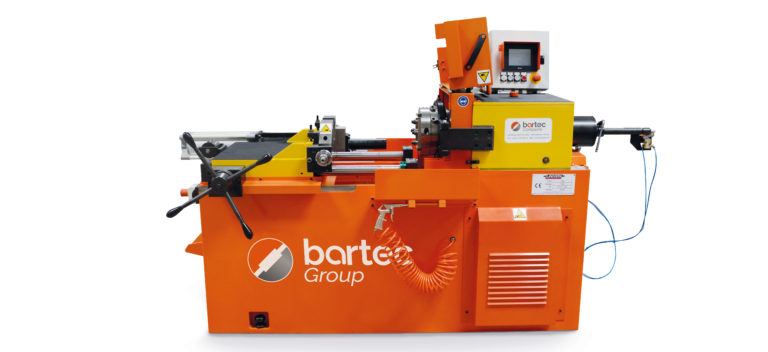
At a time when the construction industry is facing unprecedented environmental challenges, mechanical splices are emerging as an essential solution for a more sustainable future. The STARS vision, developed by Linxion The Original, perfectly embodies this ecological revolution in the construction sector.
By drastically reducing the amount of steel needed in reinforced concrete structures, mechanical splices make a significant contribution to reducing CO2 emissions. The Grand Paris Express project is a case in point, with an impressive reduction in CO2 emissions thanks to the use of couplers.
The STARS vision goes beyond the immediate reduction of carbon footprints. It proposes a comprehensive approach to sustainable construction, considering the entire life cycle of materials. This innovation not only improves the environmental performance of buildings, but also increases their safety and lifespan.
By adopting reinforcement links and the STARS vision, the construction industry is taking a decisive step towards a greener future. It is possible to reconcile technical progress, economic efficiency and respect for the environment. Our ecological vision paves the way for a new era of construction, where sustainability and innovation go hand in hand.
As we face up to the climate challenges of the 21st century, mechanical splices and the STARS vision are not just an option, but a necessity to sustainably transform the way we build and think about the future of our infrastructures.